Monday, March 4, 2019
Kuecker the company
Kuecker Logistics Group has been providing innovative material handling solutions for nearly 30 years. From fully integrating multi-million dollar systems...to retrofitting existing systems...to simply providing equipment...whatever your needs, we have the knowledge and experience to get the job done right.
Tuesday, February 5, 2019
Automated Picking Solutions & Picking Logistics
Goods to Person AS/RS: Automated Storage & Retrieval Systems
Kuecker provides automated solutions for storage and retrieval systems (AS/RS) as part of integrated solution concepts that apply the right mix of automation, software and labor for optimized productivity and throughput capacity for each operation’s unique requirements.
Horizontal Carousels
These horizontal carousels, crafted from rugged structural steel, are the most durable in the industry. These industrial automation carousels are built for long-term reliability under the most intense duty cycles and heaviest applications. Learn more about horizontal carousel automated picking solutions.
| ![]() |
Vertical Carousels
You will find that our leading edge vertical carousel storage and retrieval system is the perfect industrial automation picking solution when it comes to maximizing space utilization, productivity and efficiency in all types of applications. Learn more about vertical carousel automated picking solutions.
| ![]() |
Pick-to-Light
This paperless order fulfillment system utilizes pick-to-light, put-to-light, automated sortation, A-Frame, barcode, voice recognition and RF terminal technologies. If you’re looking for a custom designed order fulfillment system that meets your existing industrial automation needs while offering flexibility for the future, we provide a vast array of order fulfillment solutions and picking logistics systems. Learn more about pick-to-light automated picking solutions.
| ![]() |
Voice Pick
The only packaged software solution in the industry that implements the combination of voice applications, toolset and enterprise voice architecture to deliver the highest degree of control and flexibility. Learn more about voice pick automated picking solutions.
| ![]() |
Lighted Batch Carts
Custom Pick-To-Light / Mobile Batch Cart systems developed by Kuecker Logistics offer a wide range of benefits. The possibilities for cart design are endless and we are happy to work with you in determining the perfect batch picking solution for your unique operation. Learn more about lighte
More to come!
|
Wednesday, January 2, 2019
Warehouse automation trends
Labor Crunch, E-Commerce Competition Drive Warehouse Automation Trends
Staff Writer Thomas reviewJan 02, 2019
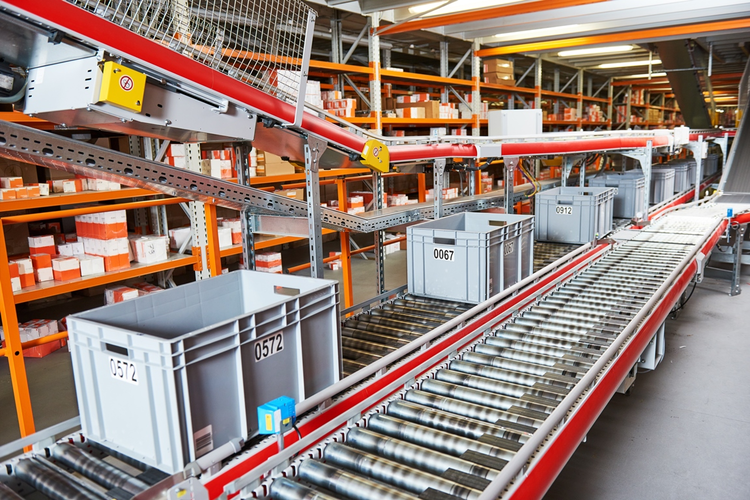
On behalf of Logistics Management and Modern Materials Handling (MMH), Peerless Research Group recently conducted its annual Warehouse and Distribution Center (DC) Operations Survey, which showed that worker skill gaps are contributing to increased warehouse automation.
Key trends spotted in 2018's survey include a rise in omni-channel fulfillment, use of warehouse management systems, and an inability to maintain a qualified workforce.
Of the 183 logistics and warehouse management professionals surveyed, 66% serviced wholesale channels, remaining the most popular option, but service of omni-channel (21%) and e-commerce (40%) channels were both on the rise for 2018, up 2% and 3% respectively. With e-commerce on the rise, warehouses are getting larger. The average square footage for a warehouse in 2018 came in at 220,800 square feet, up from 193,190 square feet in 2017.
Increased Competition, Increased Demand
In addition to a lack of qualified hourly workers, increase in demand and competition — as well as more complex customer requirements stemming from the rise of e-commerce — serve as impetus for implementing automation technologies in warehouses.
“Even if you can get orders out the door on time, that’s not good enough. It really does have to be a perfect order that gets done under a narrower time window with scarcer resources of all types throughout the network,” said Don Derewicki, a senior consultant at St. Onge Company, in a recent Logistics Management article. Of the respondents, 87% mention offering some sort of value-added service (VAS), such as special labeling or serial number control processes. This is what Derewicki is referring to — the need to go above and beyond for customers in today’s competitive landscape.
2018 saw two major shifts in productivity technologies. The use of warehouse management systems (WMS) grew to over 90% (at 93%) for the first time, while paper-based picking systems dropped to under 50% (at 48%). Similarly, labor management system (LMS) use increased to 15% in 2018.
Industrial Labor Crunch
Added efficiency, through the use of technological systems such as WMS and LMS, is partly due to industry's response to the labor crunch. Even though business is expanding, increased productivity from existing workers is critical, as it is not always feasible to hire workers on demand in order to handle increased warehouse needs.
Warehouses are struggling to find and retain skilled labor to fulfill their operations. A whopping 55% of respondents named labor scarcity as their number-one priority issue in 2018, followed by issues such as insufficient space, outdated equipment, and inadequate information systems. Plus, 19% of respondents expressed that their supply chain experienced some form of catastrophic event from 2016 to 2018.
All-time unemployment lows contribute to this problem. With increased demand and competition due to e-commerce but reduced availability of workers, automation has become a mainstay in modern warehouses. Automated systems being implemented by survey respondents include RF scanning, voice systems, advanced AS/RS, and robotics. In addition, 50% of respondents sought to improve warehouse IT — a reflection of increasing technology use. Other methods for cost reduction included improving inventory control and leveraging 3PL.
Looking Ahead
Roberto Michel, an editor at MMH, expects that operational efficiency will remain a key focus in the coming years in order to offset labor needs.
Image credit: Dmitry Kalinovsky / Shutterstock.com
Subscribe to:
Posts (Atom)